
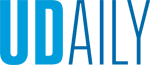
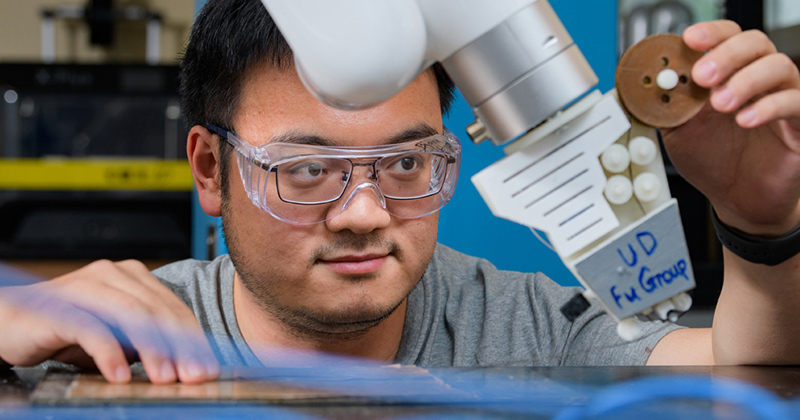
‘Disruptive’ tech
Photos by Evan Krape June 01, 2022
UD’s Kelvin Fu secures $2.5M ARPA-E grant to develop new composite additive manufacturing for vehicles
Imagine a material that can build a strong and sturdy yet fossil-fuel-free vehicle, one that could both withstand the force of getting T-boned by a bus but be light enough to offset the weight of the giant electric batteries powering it.
“We believe this is the world’s first technology of this kind that’s ever been developed,” said Kun (Kelvin) Fu, an assistant professor at the University of Delaware’s Department of Mechanical Engineering who is co-leading a federally funded project aiming to create such a prototype. “If we apply this to vehicles, no matter if they’re on the ground or flying, this can help save more energy and enable long-range travel for electric vehicles.”
The structural parts of this imaginary vehicle would be made with an intricate concoction of carbon-based fibers and cured resins, artistically arranged (actually, printed) in such a way that less material is needed, but the bonds are stronger. If this team of researchers pursuing a new way of using composites to create complex structures are successful, it would provide a cost-effective alternative for producing high-volume, lightweight and energy-efficient components for vehicles on the ground, in the air or even in space.
“Dr. Fu is brimming with exciting ideas related to additive manufacturing,” said Ajay Prasad, Engineering Alumni Distinguished Professor and Chair of Mechanical Engineering. “He has invented advanced additive manufacturing technologies to design structural and functional composites for applications including energy storage, aerospace and defense.”
The U.S. Department of Energy Advanced Research Projects Agency - Energy (ARPA-E) has awarded a project led by experts at UD’s College of Engineering $2.5 million to see if it’s possible to make those composites competitive with today’s automotive materials options. The project is one of 68 research and development efforts funded by $175 million from ARPA-E to develop “disruptive technologies to strengthen the nation’s advanced energy enterprise.”
“Dr. Fu’s success in winning this grant and others like it confirms that program managers are eager to invest in his ideas,” Prasad said. “I look forward to learning about the novel materials he will create with his additive manufacturing techniques.”

By creating something called “Composite Architected Materials Processing,” or CAMP, in tandem with new 3D-printing technology that can handle thermoset resins — which are much different than the thermoplastic polymers primarily used in 3D printing — this team of engineers aims to design not only the machinery, but also produce a prototype of a vehicle part to prove their work’s practical application. (Composite is a term used for a material made from the combination of two or more materials, which is also stronger than its components separately.)
Once they develop the CAMP technology needed to print with thermoset resin, which has a consistency more like maple syrup than the pastey plastics typically used today, then they will produce a prototype of a support pillar for a passenger vehicle. Specifically, they will create a prototype of a “B Pillar,” the support structure located between the front and back doors that runs from the roof to the bottom of the vehicle, specifically on the passenger’s side.
But instead of metal, this support pillar will be made of composite materials printed in a more geometrically-inspired way than a simple steel beam. Think of a honeycomb, for example, except each individual comb is actually thousands of layers of combs chemically fused together.
“Nobody has made a composite using additive manufacturing with continuous fibers and thermoset resins. Most of them have used thermoplastic resin,” said Suresh Advani, G.W. Laird Professor of Mechanical Engineering and co-principal investigator on the project. “The challenge is to cure these resins on the fly as they wick between the fibers during the printing process.”
Using thermoset in 3D-printing applications like this offers a technical way to create something that’s simultaneously lightweight and very strong, Fu said. But he and his team have to overcome the challenge of working with thermoset resin in this new way.
The material must cure after it is applied in a liquid form to continuous carbon fibers, which is almost the opposite process for more common 3D printing with plastic polymers. And once it’s in that solid state, it cannot go back to a melted state, Fu said.
“In our case, the 3D printer can do everything,” Fu said, hinting at future success for this novel 3D-printing technique, and the possibility of incorporating recycled materials into the process as well. “Ultimately, we want to save or reduce the carbon dioxide emissions. This CO2 reduction can come from the composite application process, but also reduced emissions of lighter-weight flying or ground vehicles. Using our 3D-printing technology can save on both, especially in the fabrication process.”
Advani explained that the novelty of this project lies in designing a printer that utilizes a nozzle to drop thermoset resin at a high temperature onto the continuous fibers in a rapid manner. The recent advent of snap-cure resins, which can solidify in minutes instead of hours, has opened opportunities to work with this unique material.
These UD researchers are not creating the fibers and resins that will be used in this new additive manufacturing process, but will purchase the materials separately. To be more efficient in their research and development efforts, Advani plans to develop a model and simulation of the wicking and curing process to help guide the ultimate design and manufacturing of the prototype.
"My role is to develop a model and simulate the manufacturing process, digitally tuning variables so we can ensure that our in-lab experiments will be successful," Advani said. "If you just relied on running experiments without understanding the physics of the material and the process, not only would it take a long time and be prohibitively expensive, but the chance of failure is much higher."
In addition to Advani’s work, the project will also benefit from computational modeling work by Xiangyang Dong of Missouri University of Science and Technology and Ling Liu of Temple University to design composite structures with the best mechanical and weight-reducing performance.
Simulations could also identify where such composite material-based structures would be most efficient, and, if the researchers can print a part quickly enough, could also significantly reduce manufacturing time and reduce the amount of energy required to produce those parts.
The lightweight element of the composite’s potential also could mean energy efficiencies for electric vehicles, potentially extending the range of a battery by reducing the overall weight of the vehicle.
The problem, however, is that these composite materials are still more expensive than metals, Advani said. Not only do researchers have to make this technology work, but they’re also going to have to prove that it can be competitive from the standpoint of price, labor and time. While ultimately the technology may not work for mainstream commercial uses like passenger vehicle manufacturing, it could be a useful alternative for smaller-scale part productions for a space shuttle, for example, Advani said.
“The question is can we cure it quickly enough and can we move these fibers quickly enough to make a composite part in a reasonable amount of time,” he said. Typically, the curing process is like baking a cake, he said — it can take hours. So if it’s going to have high-volume applications, like for the automotive industry, it needs to take minutes, not hours, to create those parts.
To address the potential future uses of this technology, Fu is hoping CarbonForm Inc., a start-up company specializing in high-performance composite additive manufacturing, will help transform the technology from concept to reality. Fu is the co-founder and chief scientific advisor for CarbonForm, which will work directly with manufacturers to develop and produce new products utilizing continuous carbon fiber and thermoset resins.
“I don’t know why no one has ever developed this technology,” said Fu. “This could allow us to fabricate some parts with much less material, and save much more energy.”
Contact Us
Have a UDaily story idea?
Contact us at ocm@udel.edu
Members of the press
Contact us at 302-831-NEWS or visit the Media Relations website